UK waste processing facility opens its doors
03 September 2012
Oxfordshire, UK, based Sheehan Haulage & Plant Hire, a privately owned groundwork and civil engineering contractor, has just commenced operation of a new multi-million pound construction and demolition waste recycling facility, which was more than five years in the planning at its 150 hectare 'Dix Pit' site on the outskirts of Stanton Harcourt.
The plant was manufactured, installed and commissioned by CDE Global, the world leading supplier of washing equipment for quarries and mines.
The washing plant contains a range of equipment from the CDE product portfolio including a feed system, AggMax portable logwasher, Prograde aggregate screens and Evowash sand washing plant. In addition the system employs full closed circuit water recycling with the inclusion of the Aquacycle thickener and GHT Filter Press.
As material is delivered to the plant an overband magnet on the feed conveyor removes any metals before it is sent to the AggMax. This involves four stages of processing on a single unit - pre-screening, attrition, trash removal and aggregate dewatering.
The pre-screening stage allows for any -5mm particles to be liberated and delivered to the sand washing phase. The +5mm aggregate material enters the integrated Rotomax logwasher and is subjected to a high level of attrition from the twin shaft machine. This further liberates more -5mm material while also floating off any lightweight contamination at the rear of the unit. This is subsequently dewatered on the trash screen and while the trash material - plastics, polystyrene, rubber, wood - is discharged into a bay the -5mm material and waste water are also sent to the Evowash sand washing plant to maximise recovery of the sand fraction.
As the scrubbed aggregates are discharged from the Rotomax they are delivered to a dewatering screen where they are given a final rinse before being sent to the aggregate sizing phase. On this project a Prograde P275 dry sizing screen produces 4 recycled aggregate products - 5-10mm, 10-20mm, 20-40mm and +40mm. The -5mm material is washed to produce two recycled sand products via the Evowash 102 dual sand plant.
The water treatment phase first involves the Aquacycle thickener which receives waste water from the Evowash containing the -63 micron particles. The Aquacycle design allows for high rate settlement of these fine particles to the bottom of the thickener tank while the recycled water overflows to a concrete water recirculation tank before being recycled to the washing plant. A lightweights removal screen ensures that any material such as polystyrene that has not been captured does not re-enter the water circuit.
The settled sludge from the Aquacycle thickener is then delivered to a concrete buffer tank before being sent to the GHT Filter Press to maximise water recycling. In this instance the filter press is made up of 140 plates which press the sludge at extremely high pressure to remove the maximum volume of water. The waste material is then compressed to a filter cake containing 90% dry solids content which is dropped from the filter press into a bay below.
Approximately 50% of the material is used by the Sheehan Group on its own construction and civil engineering projects with the remaining 50% sold to the local private construction market.
CONNECT WITH THE TEAM
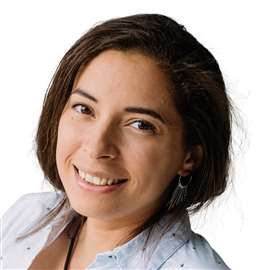
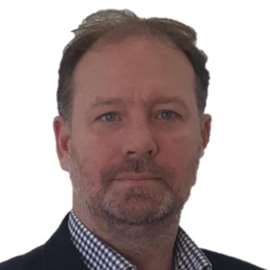