Soaring prices mean it's a boom time for scrap
11 June 2008
With the ongoing growth in recycling, and soaring scrap metal prices, sales of scrap handling equipment are also buoyant. D&Ri reports on this specialised sector
The price of scrap metal is soaring and recycling rates are climbing so it stands to reason that the need for materials handlers is also booming. The leading specialist manufacturers in the sector who design and build machines specifically for these applications confirm this.
Terex Fuchs general manager Ron De Vries told D&Ri: “ The market is extremely strong. In 2008 we plan to build and ship 35% more machines than we did last year, and even so will not be able to meet the demand that is out there. It is the high price you can get for scrap metal that is driving this as well as the growth in recycling. Because of the strength of the current market and the continuing drive to improve recycling rates around the world, I do not see this demand declining”
“Scrap handling is by far the biggest segment of our operations for the lighter applications. Outside of Europe, countries like the USA and Eastern European countries that have recently joined the EU are now taking much more notice of the recycling concept.”
Currently, all Terex Fuchs products are manufactured in Germany and then shipped to its customers around the world, but being part of a major multinational company with manufacturing facilities in a number of countries does offer one benefit that the company is in the process of taking advantage of. Mr de Vries said: “We have been looking at producing locally for local needs for some time. We have been pretty successful in the USA, and demand for our equipment there is extremely high. The current weakness of the US dollar has therefore been a cause for concern for us. As a result, we plan to start production of some of our more popular models in a Terex facility in the USA before the end of this year.”
“Availability is a big factor in the purchasing decision at the moment because of the high demand,” Mr de Vries said. “If you can supply a new machine quickly, then you can get a good price for it. Of course, you have to be able to offer the quality, reliability and performance necessary for the application.”
Currently, the largest machine in the Terex Fuchs line-up weighs in at 77 tonnes, so does the company have any plans to go heavier? Mr de Vries answered: “No, the machines at the heavy end tend to be used in portside applications, and this is not an area of great interest to us. Our primary target market is in the lighter applications where we are already pretty successful around the world.”
Keeping it simple
German manufacturer Sennebogen is another such equipment specialist. Its basic philosophy is to ‘keep it simple’, avoiding electronics as much as possible and ‘purpose-built machines’. There currently are seven models its Green LIne of machines, weighing from 22 up to 95 tonnes, but within this there are multitude of possible variants, depending on the customer and application requirements. The company offers what it claims to be the widest range of variants in the industry – wheeled, crawlers, electric, diesel, elevating cabs, pedestal cabs etc, with the bulk of the assembly being to order.
The key point of note is that Sennebogen machines are not excavators that have been adapted for material handling – they have been custom designed specifically for the role [as indeed is the case with Terex Fuchs. They are used in materials handling applications in four main sectors – recycling, ports, forestry and sand and gravel, with recycling being by far the largest of the four.
According to Alfred Endl, Sennebogen’s president – sales & operations: “With the current high prices for steel and other metals, the recycling sector is a growing market at the moment but from a high start point. This is predicted to continue for the next two years at least, fluctuating at this high level, In addition, there are markets such as China and India where the demand for steel will continue to grow, so the demand for scrap will remain.”
The company is currently erecting a third plant in Straubing to build the larger Green Line machines as well as its crawler cranes, since it is currently running at full capacity. However, the main reason for this development is to provide a facility better suited to the manufacture of the two largest green line machines and the company’s range of crawler cranes.
Mr Endl said: “The main market drivers in the scrap handling sector are productivity, efficiency and reliability, because in many applications the machine are working around the clock and very often, the scrap handler is the key to the whole operation. High efficiency/productivity is also essential. This matches our philosophy of avoiding the use of electronics in its products, not having to many modes on its machines and making them very service friendly. The machine should be able to work 24 hours a day – sometimes the company’s machines reach 6,000 of 7,000 hours a year.”
“Increasingly, ergonomic factors are also coming into play. With this in mind, we has improved the driver comfort of its D Series machines. The Max Cab has greater space and comfort inside, air conditioning and improved visibility around the machine, since safety is also becoming a greater concern,” he went on.
“Where product development is concerned, we are mainly now working on changing over from the C Series to the D Series and is carrying this out on a model-by-model basis. We are also looking at new applications for its equipment. The 880 is our newest machine as well as our biggest ever, but we currently has no plans to produce anything larger. The 880 has a 33 m (108 ft) boom and a capacity of 10 tonnes at that reach – that is considered big enough at the moment.”
He continued: “Electric motors are becoming a greater feature on material handlers because diesel engine fuel consumption is becoming a concern, with even US customers becoming sensitive to this issue since fuel costs, while still low by European standards, have increased by 50% on last year. While it is more expensive to buy, where life-cycle costs are concerned, it can be a real advantage.” He said that the performance of the hydraulic systems are softer, the motor will run for between 40,000 and 50,000 hours and operating costs are lower since maintenance is low - there is no oil, coolant etc. Mr Endl estimates suggest that with an electric motor, savings of up to one third of operating costs can result. He believes that Sennebogen is the only manufacturer who can supply all of its models powered by an electric motor.
The full line approach
While there are machines that are custom designed and built as waste handlers, there is another option available from full line construction equipment manufacturers.
German manufacturer Liebherr offers six wheeled excavators tailored for the materials handling role from the 21 tonne A316 up to the 127 tonne A 974 B Litronic, along with five crawler models from the 31.5 tonne R 924 C Litronic to the 100 tonne R 954 C Litronic High Rise. And of the course the company’s range of wheeled loaders also find applications in this field.
New to these machines is Liebherr’s Vario Lift Plus System, which allows the lifting and reach of the machine to be optimised for specific applications. This is achieved through the provision of preset mounting holes on the boom and upper carriage to allow the hydraulic cylinders to be adjusted to provide additional reach or lifting capacity.
JCB is another who has identified that the recycling sector offers considerable potential and has devoted considerable resources to the sector in recent years. Jonathan Garnham – general manager, waste, recycling and demolition, told D&Ri: “Recycling is moving at a pretty astonishing rate at the moment. JCB has been selling into the sector really from when we began, but it became a target about six or seven years ago. Within that, scrap metal processing is one of the top sectors - scrap has a high value, especially at today’s prices, and is one of the easiest to recycle, so the metals industry is very exciting.”
He went on: “We now have a separate department that focuses on the waste sector and we have a product range called Wastemaster that focuses on that sector that was updated last year. It consists of more than 25 different models so we have a full line-up, from the very small to the very large. It is that complete range that people are looking for now.”
He went on: “We are really going to ‘up the anti’ as far as the US market is concerned and put a major focus on as it is a also a very exciting market. So when it comes to waste and recycling it really is a global market for JCB.”
JCB does a number of things to its basic machines to make them suitable for this market such as elevating cabs or fixed raised cabs on excavators.
However, MR Garnham explained: “It is not always the case of taking a standard JCB machine and modifying it for this market – a number of the Wastemaster material handlers have been designed specifically for this application. And before we do take a machine designed for the construction application and add all these features, a great deal of testing is carried out to make certain that it is suitable for the role.”
The biggest wheeled machine in the range is the JS200, which weighs in at just over 23 tonnes with a standard cab and 26 tonnes with an elevating cab. Where crawler units are concerned, the largest is the JS220, which with full Wastemaster specification and an elevating cab weighs 25 tonnes
According to Mr Garnham, customers currently have a number of requirements, such as productivity, safety and smoothness of operation. The cost of ownership and running costs also major factors since these machines will operate for up to seven years. Given the nature of the work these machines carry out, reliability is crucial, allied to a high standard of service backup.
The majority of the machines JCB supplies are wheeled, but its sales are not exclusively wheeled. Crawler versions make up around 30% of its sales. There are applications where movement around the facility is not required or the surface is soft, or where the greater stability offered by a tracked machine is attractive. They have a lower centre of gravity and have a very solid footprint.
Currently, JCB is working to develop a Wastemaster telehandler that it sees being used in filling containers. In many recycling centres, metal waste is packaged into pallet-type loads that are then transported by container lorry for further processing. The telehandler’s ability to telescope out loads to ensure efficient packing is an obvious benefit.
Mr Garnham finished by saying: “What the future holds for the sector in terms of volume is very hard to identify since obtaining hard and fast figures is very difficult - nevertheless it is unquestionably going to grow. JCB will be busy, that’s for sure.”
MAGAZINE
NEWSLETTER
CONNECT WITH THE TEAM
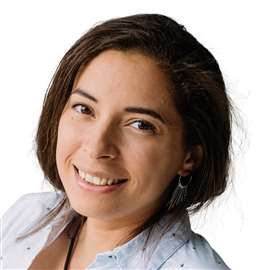
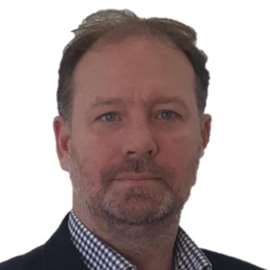
