Setting the record - CDi implodes Ocean Tower on South Padre Island, Texas
05 February 2010
US contractor Controlled Demolition Inc set a new height record for an explosive demolition in December 2009, when it brought down the 116 m (380 ft) reinforced concrete Ocean Tower on South Padre Island in the Gulf of Mexico. D&Ri reports
Ocean Tower was intended to provide high end accommodation in the shape of 151 luxury apartments on South Padre Island. However, two years after construction began the building's foundations began to sink, resulting in the structure taking on a list and halting all further construction activities. In the end, the only decision left was for the structure to be demolished.
Options ranged from conventional, non-explosives demolition of various portions to full explosive demolition of the entire complex, including combinations of the two. CDI selected conventional pre-demolition of half of the parking garage and explosive demolition of the balance of the garage and tower. High winds at South Padre Island (SPI) dramatically reduce viable work days at upper elevations and use of a crane was simply out of the question for this reason. The long-term placement of personnel and light equipment for light mechanical demolition of the upper tower floors also presented risks to workmen and to the public from flying/windblown debris that were not acceptable. It was considered better to select "the right day" to bring the entire tower down in one go while eliminating the risk to persons by evacuating an acceptable area and mitigating the risk to adjacent third party properties through careful preparation and exacting execution.
After months of preparation and planning work, Controlled Demolition Inc (CDI) set more than a tonne of explosive charges across the building, using more than 2 miles of detonating cord. At 9.00 am on Sunday 13th December the charges were set off. The building took just 15 seconds to fall, leaving a pile of concrete and rebar containing more than 50,000 tonnes of debris to be cleared up.
Meeting the challenge
The 3-story parking garage was an unbonded tendon, post-tensioned reinforced concrete structure. The post-tensioning insinuated itself structurally into the lower three floors of the 33-level tower that was a post-tensioned/cast in-situ reinforced concrete hybrid structure. From the 4th floor to the 33rd slab at elevator penthouse roof level, the balance of the tower was cast in-situ.
The two stair cores and the elevator core of the tower represented the most heavily reinforced commercial construction CDI had encountered. The only more heavily reinforced construction it has encountered was in the nuclear industry where CDI has been active demolishing heavily reinforced structures both domestically and internationally.
The failed, yet standing Ocean Tower structure was challenging because the pre-existing damage meant that loads were not being transferred through the remaining structural elements in a fully predictable, much less programmable fashion. This uncertainty required CDI to maintain a greater Factor of Safety (FOS) from a structural preparation standpoint, limiting the amount of pre-preparation it could perform prior to the actual implosion. That meant having to do "more work" during the implosion sequence than would be the case with an undamaged structure that could be properly defined from a structural standpoint.
There were up to six curtains of rebar in the elevator and stairwell cores, and the concrete used in the structure had cylinders broken at 28-days curing time well in excess of 10,000 psi. The original concrete spec for the walls was 6,000 psi. The massively reinforced, cast in-situ upper portion of the structure had progressive failure tendencies far more resistant than the unbonded, post-tensioned garage and lower post-tensioned floors of the tower. The differential failure propensities provide for a challenging analysis of likely response during catastrophic progressive failure induced by CDI's Implosion Plan.
The sandy soil conditions and high water table created an ideal environment for energy transmission from the arrival of debris at grade during the implosion sequence into the multi-million dollar homes built immediately adjacent to the tower's north side. Mitigation of vibration was therefore a key element to CDI's Implosion Plan and involved the extent of pre-demolition of the 3-story parking garage, treatment of debris resulting there from, impact upon and potential advantageous use of pile caps/piling in the garage footprint above and beyond the selection of number of blast floors in the structure and the implosion timing for detonation of explosives on various levels.
The nature of the Ocean Tower force system did not permit test blasting of columns due to the existing damage in much of the structure.
The massively reinforced stair and elevator cores were selectively modified with explosives to create openings to which CDI could move concrete during the final implosion sequence. The robust Ocean Tower construction required that all of these openings be blasted, and this pre-blasting, in effect, gave CDI the opportunity to "test blast" the stair and elevator core walls.
There were three reasons to pre-demolish the garage.
By pre-demolishing the eastern half of the garage, CDI eliminated the possibility that the anchors from the unbonded, post-tensioning tendons could suddenly release as the building fell. Sudden release of anchors can cause them to fly considerable distances and cause injury or damage.
By pre-demolishing the garage, CDI opened the fall area up so that debris from the tower would directly impact the garage pile caps, allowing much of the impact energy to be transmitted downward to lower strata, reducing the amount of energy available to create a Rayleigh surface wave that could damage the adjacent structures and infrastructure.
Finally, pre-demolition of the eastern half of the garage permitted pre-processing of that debris to shorten the duration of post-implosion cleanup.
Explosives were placed on the 1st, 2nd, 3rd, 7th, 11th, 17th, 21st and 26th floors. The primary purpose was to prepare the debris from the structure to fall within the available site, rather than having the rigid elevator and stair cores reach outward into the protected sand dune areas to the east. Working on additional floors also helped mitigate the type and amount of vibration from arrival of debris at grade.
The implosion took place at 9:00 a.m. on Sunday, December 13th, with perfect results. Post-implosion surveys revealed that there was absolutely no damage whatsoever to the multi-million dollar beach homes immediately adjacent to the Ocean Tower site. Debris processing has already begun and the site is expected to be cleared sometime in March. CDI used a total of 705 kg (1,550 lb) of explosives in the final implosion sequence, along with 4,358 m (14,300 ft) of detonating cord to initiate explosives in the 1,841 holes that were loaded on the eight blasting levels of the structure.
CDI's felling of the structure did not compromise the protected Dunes area at all, and the local authorities are pleased with the results, as is our client.
The implosion generated 55,000 tons of debris. Additionally, there were 15,000 tons in the portion of the garage that was pre-demolished, generating a grand total of 70,000 tons (or 35,000 cubic yards). All concrete and rebar will be recycled, with rebar taken to a scrap site for processing at the Port of Brownsville and the concrete being crushed and screened on South Padre Island for reuse/sale by CDI's subcontractor.
It took less than 20 minutes to remove dust from Texas Route 100 adjacent to the building to open the highway for traffic to the north end of South Padre Island.
CONNECT WITH THE TEAM
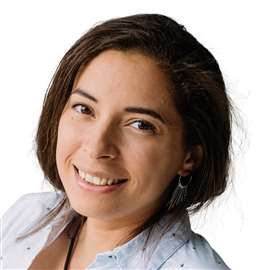
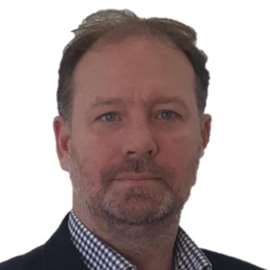