Screening - the finest of margins
27 April 2021
Allu has launched crusher buckets for 10 to 38 t machines adjustable for 13 different discharge sizes, alongside the screening buckets it has produced for the past 30 years.
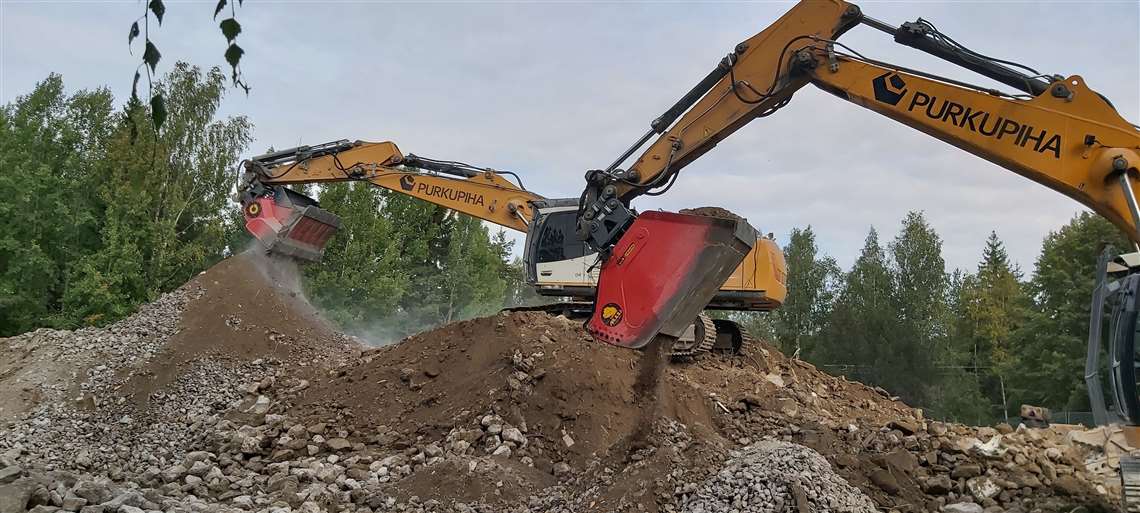
The Finland-based manufacturer said that placing two solutions side by side provides demolition sites with increased capacity, saving both time and money.
A customer in Finland became the first to test the crusher and screener side by side for demolition. A sieve and crusher bucket chain for handling powdered concrete, and at this site, 85% percent was screened and partially crushed through a screener crusher and only the excess very hard material was crushed with a crusher bucket.
Maximum fraction size
“The demolition concrete was treated after pulverisation with two Allus” said regional sales manager Ilpo Ellonen.
“The excess obtained from the screener crusher bucket visible at the front was crushed to a 90 mm (3.5 in) fraction with a crusher bucket. Thus, a total of about 5,000 t passed through two buckets. The demolition of two residential buildings of two storeys each produced a total of about 5,000 t of concrete. The maximum fraction size achieved in the pulverisation was 400 mm, which is a maximum good input feed size for the Allu crusher bucket. The jaw is reversible, which enables fast and easy recovery of from possible blockages.”
The demolition phase took three weeks. At the time of the visit, between 600 and 700 t of concrete waste were still untreated. In the fourth week, there was still a run-off of crushed concrete for use at the bottom of the forest road. The purpose of the entire process is to recycle concrete waste at Allu into stone aggregate for reuse, which replaces the need to use virgin aggregate providing an environmentally sustainable solution.
Allu said the throughput of material from the screener crusher bucket is many times higher than with the crusher bucket, so the goal is to get the fines out as accurately as possible by screening so that the amount of material to be crushed is kept to a minimum.
EvoQuip launches self-contained units
EvoQuip launched the Falcon Range of finishing screens to its product portfolio at the end of 2020. The Falcon range consists of the Falcon 1220 and Falcon 1230, providing a solution for scalping, screening and stockpiling in self-contained units.
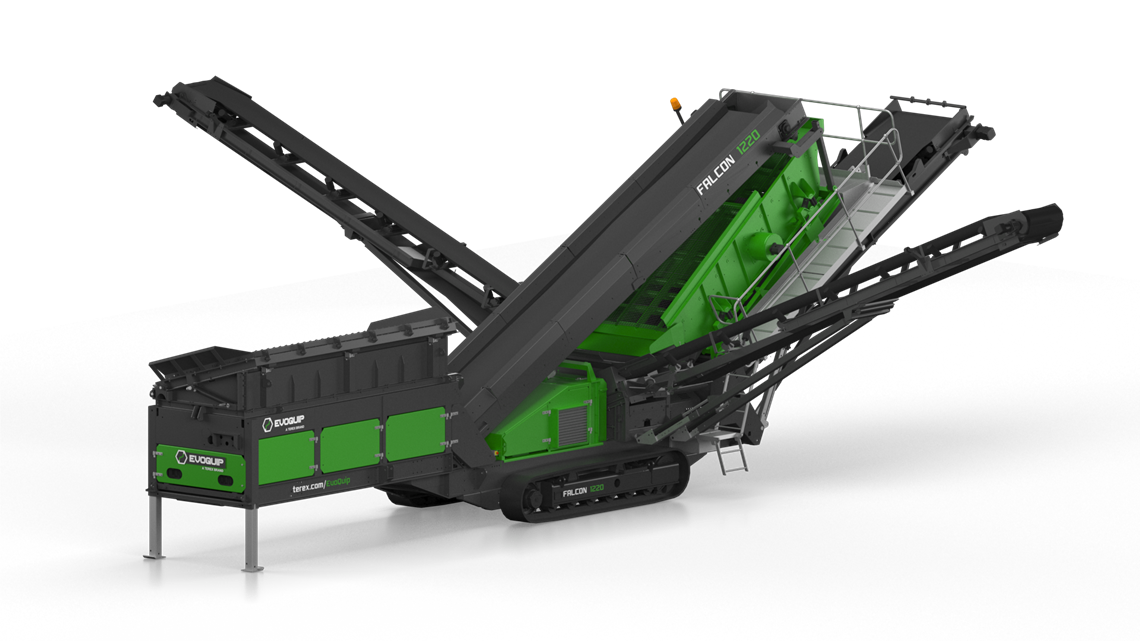
“This enhances the EvoQuip product offering and results in us having a more comprehensive product portfolio that will improve our versatility and make us more competitive in the marketplace,” said business line director Barry O’Hare.
“We are confident that these highly aggressive finishing screens will open up new opportunities for EvoQuip customers globally.” The Falcon range, with what EvoQuip – a brand of global manufacturer of material processing products Terex Corporation – calls its exceptional screen angle range, is said to provide efficient classification of fines and is ideal for multiple applications including processing demolition waste.
In keeping with the EvoQuip range, both the EvoQuip Falcon 1220 and Falcon 1230 are compact machines said to offer operators rapid set up and tear down times.
The Falcon 1220 features a 3.65 x 1.5 m (12 x 5 ft) double deck incline screen with remote tipping reject grid, hydraulic screen tensioning of bottom deck and three on board hydraulic folding conveyors as standard, with the option of adding the double deck vibrating grid.
Inclined decks on the Falcon 1230
The screenbox on the Falcon 1230 features three inclined decks giving a large screening area of 15.8 sq m (170 sq ft) to provide efficient, high-capacity screening, even at small fractions. The fourth product conveyor has variable tilt and side slew to accurately discharge material for recirculation and stockpiling. The screenbox features quick wedge tensioning (top and middle deck), access holes and bottom deck hydraulic tensioning system to reduce time required for mesh changes.
The Falcons come with the T-Link telemetry system fitted as standard, providing the customer with real-time information on the performance of their machine, meaning effective machine management and maximising uptime.
Kleemann’s updated screen programme
German manufacturer Kleemann has upgraded its screen programme so that its Mobiscreen MS 1202 and MS 1203 are available with two or three screen decks and have screening surface areas of 12 sq m (129 sq ft) in the upper and middle deck and 11 sq m (118 sq ft) in the lower deck.
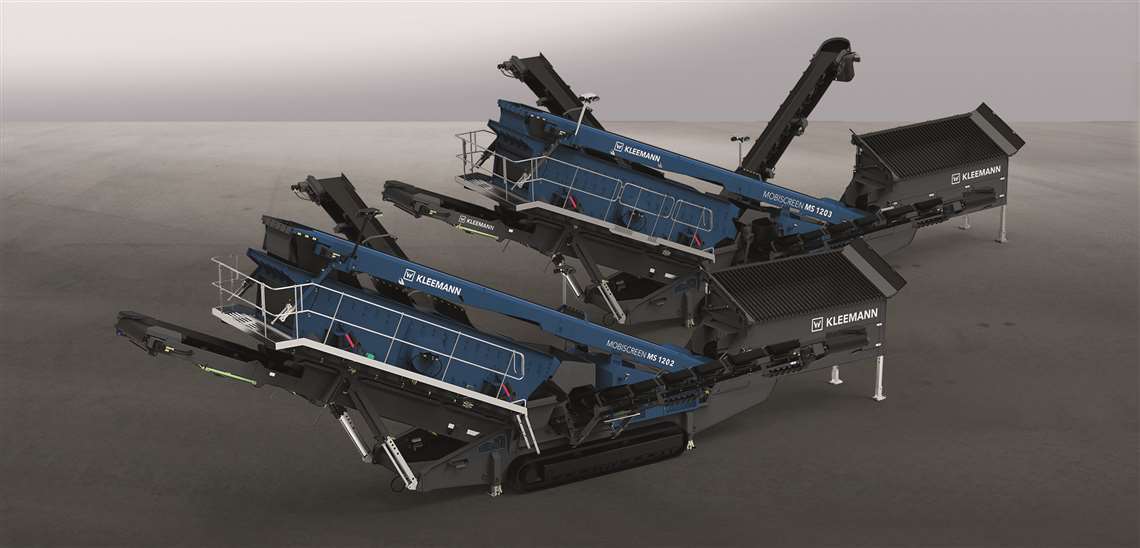
“To achieve these high outputs, the material flow must be well designed,” said Aiko Fischer, product manager for screening plants at Kleemann, which is one of five brands within the Wirtgen group.
“We have generously dimensioned the feed hopper with a holding volume of 10 cu m (353 cu ft). This akes feeding both with a crushing plant and a large-wheeled loader possible.
“The large hopper volume ensures continuous material supply to the screen. Correspondingly wide feeding and discharge conveyors guarantee an unobstructed material flow over the screen. The high-torque diesel engine also ensures that the plant does not run out of steam.”
Adjusting the screening angle
“Apart from the pure performance data, we should not forget the most important thing: the adjustability of screening angle and amplitude to the different feed materials and their properties. Besides the selection of the suitable screen surface, the correct selection of these parameters ultimately decides the screening performance and product quality”, continues Fischer.
Both screens can be combined with the crushing plants from the Kleemann EVO series and its PRO series. “The smaller the separating cut and the higher the required final product amount, the larger the screening surface must be,” said Aiko Fischer.
“It’s really quite simple.”
As with other screening plants in the Mobiscreen series, the MS 1202 and MS 1203 are driven by hydraulic power units. The dual power option also allows the screens to be driven by electric power only.
For flexible application, Kleemann offers a large selection of screen surfaces with different mesh shapes – square, rectangular or harp-shaped – as well as the correct characteristic, for example steel or plastic.
To ensure that this flexibility relates not only to the screen applications but also to the different job sites, good transport properties and fast set-up and dismantling times are very important. The MS 1202 and MS 1203 can also be transported in one piece.
The challenge of crushing fine material
Crushers can be used on a huge selection of materials in a range of applications, from recycling to crushing natural stone.
Often the crusher is fed with a high proportion of fine material, which unnecessarily passes through the crushing process, increasing wear and energy consumption while reducing throughput.
As a remedy, a bar mesh is normally used for pre-screening. However, if the fine material is damp and cohesive, it can quickly clog up the mesh screen and ends up passing through the crusher anyway.
That is why Rubble Master launched the patented RM Active Grid, a new highly efficient pre-screen that is said to increase material throughput by up to 30% and reduce wear.
Construction and demolition waste
High levels of fine material in the crushing box can reduce the efficiency and profitability of the crusher.
Construction and demolition waste is just one example where a high proportion of fine particles can be found in the feed material. If a pre-screening system is not used, all the material ends up in the crusher, irrespective of particle size, often passing through the whole crushing process.
Unfortunately, the fine material causes unnecessary wear to the hammers, impact plates and wear plates in the crushing box, as well as higher energy consumption in the form of diesel or electricity, because the rotor is subjected to higher stress. The result is higher running costs because the hammers and wear plates need to be replaced more frequently, and maintenance cycles are shorter. This not only reduces the efficiency of the crusher, but also reduces profit, because material throughput is lower, but running costs are higher.
Rubble Master, which has been producing crushing and screening machines for 30 years, developed the RM Active Grid to solve these problems. It consists of rigid and moveable sections of bar mesh that feature a special configuration. The vibration of the vibro-channel causes the product to oscillate, so it does not need its own drive system. Efficiency is also said to be increased thanks to its self-cleaning effect. The fine material can then bypass the crushing box onto the main discharge belt or be discharged on a side discharge belt.
The RM Active Grid is available for RM 100Go! and RM 120X crushers.
Dual-certified TTS 518
Terex Ecotec, part of the Terex Corporation, has expanded its trommel offering with the launch of the TTS 518. The company’s smallest trommel to date, the TTS 518 has been intuitively designed offering operators application flexibility, production rates and serviceability. Fully equipped with a Stage V/Tier 4 engine (dual certified) and the latest intelligent screening technology, the TTS 518 delivers a superior and cost-efficient end-product. Suited to small to medium sized operations where space may be limited, the TTS 518 is available in both tracked and wheeled variants and can screen a variety of material.
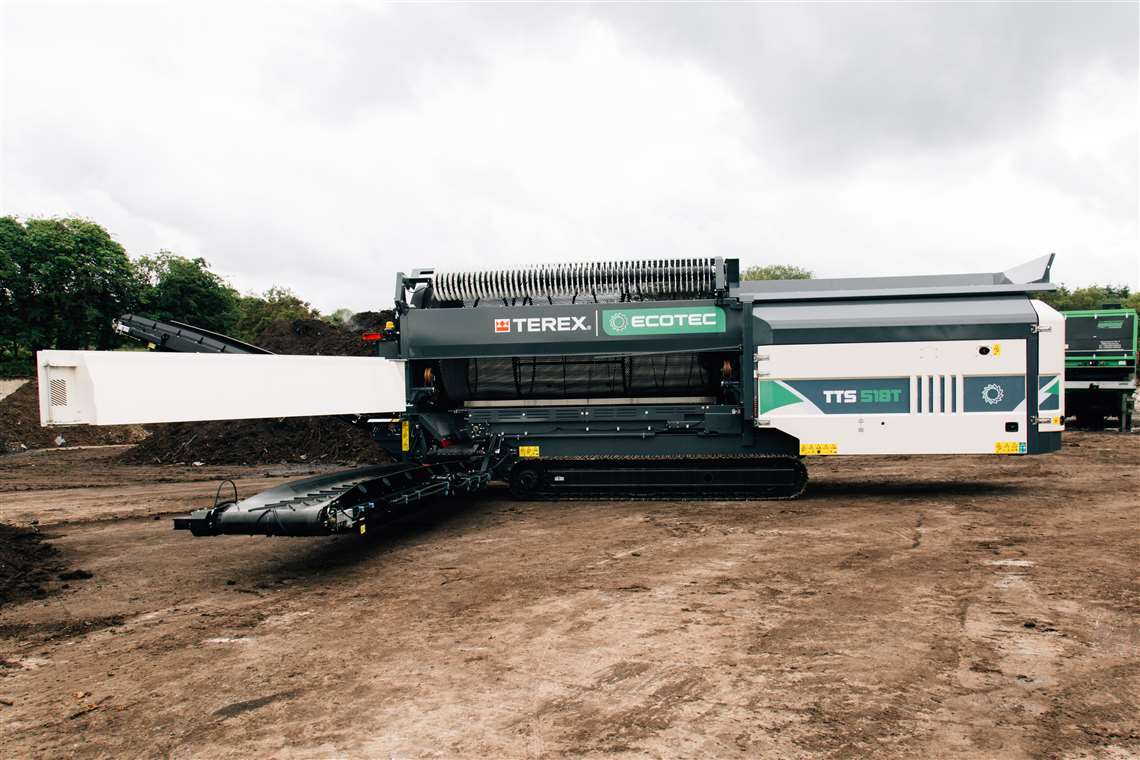
“The TTS 518 trommel will complement our strong range of trommels already in the market,” said international sales director Conor Hegarty.
“Inspired by the successful TTS 620, the TTS 518 has been designed as an entry level machine where lower volumes and smaller machine footprint are required.
“It is more compact without sacrificing key features the TTS 518 benefits from low operating costs and comes with the latest engine technology complying with Stage V emissions standards.”
The TTS 518 shares the same control system used on the TTS 620, allowing the operator to configure the machine to suit the required application. The feed control system continually monitors the machine adjusting the feeder speed to optimise screening performance and throughput.
Providing a total screening area of 23 sq m (27 sq ft), it is fitted with a 1.8 x 4.7 m (6 x 15 ft) horizontal drum with spiral design.
The TTS 518 has been designed to accept several other trommel manufacturers’ drums, enabling it to integrate seamlessly into an operators existing fleet.
European Union approval
An adaptable trommel suitable for all market conditions, the TTS 518 is available as a full European Union Whole Vehicle Type Approved wheeled unit or as a tracked unit where increased site mobility is required.
Xcentric Ripper International has added the XS60 to complete the Xcentric Screener buckets range, for hydraulic excavators from 18 to 70 t.
The company describes the Xcentric Screener is a high-performance screening bucket of the rotating trommel type. In its manufacturing several variants have been combined.
A 12-sided polygonal trommel, shakes the material inside more efficiently; the hexagonal profile of the screening mesh, which the company believes makes it the best choice between maximum yield and more homogeneous screening.
The transmission between the main hydraulic motor and the trommel is done by a time belt, which can transmit a great torque, besides being free of maintenance and/or periodic tensioning; and the Powerboost system, which applies vibration to the trommel while turning, increasing production.
CONNECT WITH THE TEAM
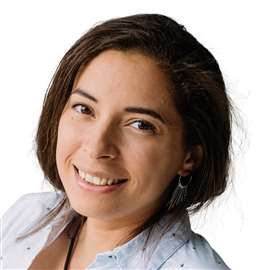
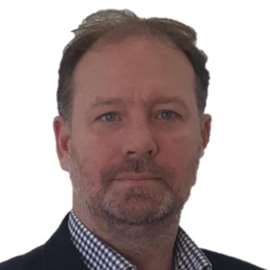