Remote control first for North America
13 January 2009
US-based Zubick Ltd., Scrap Metals has retro-fitted a rubber-tired Sennebogen 850 M with a remote control to feed its new stationary shear.
A single operator sitting in a central tower now controls the shear and 850 M material handler - the first time this has happened in North America.
"When we were spec'ing the purchase, the possibility was raised of having one operator run the shear and material handler in a remote control application," said George Zubick. "So we approached Sennebogen with a simple question: This is what we want to achieve - is it possible? When they said, ‘Yes, it is,' we took the plunge."
Thanks to the simplicity of its design and operation - absence of an on-board computer and the easy-to-maintain hydraulics, added Mr Zubick, retro-fitting the remote control was essentially a ‘plug and play' operation.
Sennebogen's engineers in Germany designed it and tested it over there. All Zubick had to do was hook up the connections under their guidance. Once the system arrived at the company's yard it took one day to install and another two to test it and get the operator used to the application.
Located in a tower that overlooks the shear and material handler, the remote control system consists of an operator's chair identical to that inside the 850 M. There is also a joy-stick that operates the material handler and a control panel at the operator's left hand to control the shear.
With the 850 located on his right side, the operator runs the material handler just as if he were inside it. Fitted with a Bateman 1.5 yd3 (1.15 m3) Mag-Grab, the 850 M feeds the shear in a continuous cycle with what George Zubick calls a "dog's breakfast of unevenly sized feedstock."
Choosing a rubber-tired machine, according to Bruce Zubick, also has benefits because it can move around the company's yard when the need arises. "If for whatever reason the shear isn't running, the operator can turn the remote control button off, jump in the 850 and travel to another site and go to work.
"It's down to maximizing your uptime and efficiency by maximizing your mobility and flexibility. Minimizing your costs doesn't hurt, either," he added.
MAGAZINE
NEWSLETTER
CONNECT WITH THE TEAM
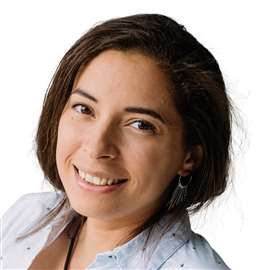
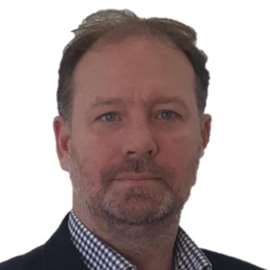
