Paper free zone - Lee Group demolishes Dartford paper mill
20 July 2010
Many industrial sites around the UK have reached the end of their useful life as processes evolve and new technologies make others redundant. The Arjo Wiggins paper mill in Dartford is just one example of one such installation that has fallen foul of changing times. It was used to produce carbon paper, once an office staple but now rarely used. As a result, it ceased operation in 2009 and Arjo Wiggins took the decision to demolish the site and sell the freed-up land on for redevelopment for residential use.
Lee Group won the contract to carry out the job, and arrived on site early in 2009. The company is now well into the contract and expects to complete the demolition work on time at the beginning of September.
The first challenge was asbestos remediation. Given the nature of the processes carried out in the mill, there was a considerable volume of heat insulation in the various steel frame and reinforced concrete buildings on the site. A team of 30 Lee personnel was brought on site for the work and in total removed 1,100 m3 (1,400 yd3) of this dangerous substance, which took 40 35 yd3 lorry loads to remove from site.
Soft strip turned out to be a major feature for the company, since unusually for an industrial demolition site, almost all the equipment and fittings required for its day-to-day activities had been left on site. It was as if the workforce had simply left the mill at the end of one day and never returned. In one of the buildings Lee found, and had to remove, more than 400 tonnes of spare parts and other equipment, from nuts and bolts through to forklift trucks and power washers.
The structures on the site were a mix of steel framed and reinforced concrete building, which in themselves were straightforward to demolish. It was what they contained that created more of a challenge. All the process plant remained in situ, including the heavy rollers used in the production process. All this equipment had to be cut up and then dragged out of the buildings using a 70 tonne excavator before demolition of the structures themselves could take place. To date, Lee has sent 2,500 tonnes of metal for recycling and expects that the final total will reach 4,000 tonnes.
During the demolition phase, 20 Lee personnel are on site, using a mix of equipment, from a Kocurek modified Komatsu PC800 high reach with a maximum pin height of 43 m (141 ft), a 70 tonne Volvo, two tonners a 36 tonner and two 24 tonne machines. In addition, a loading shovel and a telehandler are on the site, while a Metso Lokotrack crusher has just arrived to crush the concrete debris that will be used to level the site off once demolition is complete.
MAGAZINE
NEWSLETTER
CONNECT WITH THE TEAM
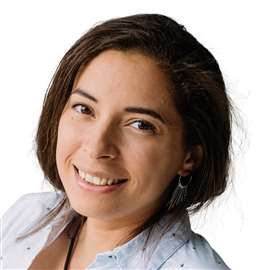
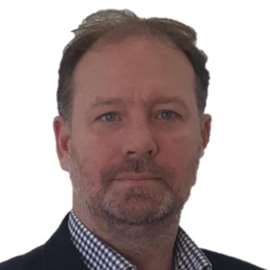
