Liebherr: 4 hurdles to overcome before hydrogen combustion engines go mainstream
14 August 2023
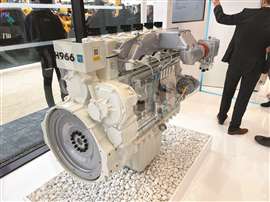
The prospect of construction equipment running on low-emission hydrogen combustion engines is now on the horizon.
That’s thanks to a considerable amount of investment and research from engine manufacturers and construction equipment OEMs, which are racing to come up with different technologies to power machines as the sector moves away from fossil fuels.
Among those companies is Liebherr, whose managing director of its combustion engine business unit, Stefanie Gerhardt, spoke to Becky Schultz, senior editor, Diesel Progress/New Power Progress in a new podcast.
Gerhardt asserted that hydrogen combustion engines can be used everywhere where electrically powered machines and hydrogen fuel cells reach their limit. And she suggested that they would be particularly useful in construction applications where economy, robustness, and high performance are required.
The performance of prototype hydrogen combustion engines is already on a par with conventional diesel engines, she said.
“From our point of view, the hydrogen combustion engine is seen as a trailblazer for rapid decarbonisation as it largely combines the advantage of an existing combustion engine technology with the option to be able to offer an emission-free powertrain,” she added.
But there are nonetheless hurdles before construction sees the widespread adoption of hydrogen internal combustion engines.
In her conversation with Schultz, Gerhardt listed four such hurdles before the technology can go mainstream. They are:
1) Combustion technology
Gerhardt pointed out that while diesel burns in a stable and controlled manner, hydrogen combustion is more sensitive to mixture quality and local hotspots, which can lead to abnormal combustion such as pre-ignition, knocking or backfires, all of which need to be avoided to ensure an engine’s reliability.
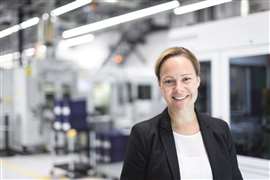
Fortunately, Liebherr has already made considerable progress on this front, she said. “We have started to test hydrogen internal combustion engines three years ago. So we started very early with this investigation. We accumulated lots of experience in how to optimize the storage, the injection and the combustion process by testing several technologies.”
Areas that Liebherr has refined include optimising the hydrogen-to-air mixture, piston design, the turbo charging layout and ignition setup. The company has been working on two different hydrogen injection technologies – a direct injection system similar to the way conventional diesels work, and a port fuel injection system (which sees hydrogen injected into air intake port).
Any challenges on the combustion front are likely to be relatively shortlived. Gerhardt said that Liebherr would kick off “series production” of hydrogen engines by 2025, before which it will further develop and validate adaptations to make engines run efficiently like turbochargers, ignition systems and exhaust gas regulation systems.
2) Lubrication
Another technical challenge involved in developing hydrogen combustion engines comes in ensuring that they are lubricated correctly. While hydrogen combustion produces water as a byproduct, the engine still needs lubrication with oil. And research is still underway to find out the best type of oil required for that process. “We are working in close collaboration with oil formulators and developers to make sure the perfect match between the lubricant and the engine will be found,” Gerhardt says.
3) Availability of hydrogen fuel
Chief among the challenges when it comes to using hydrogen combustion engines in the construction equipment of the future is the availability of the fuel itself. “The hydrogen supply network is not yet developed enough so that every customer who wishes to operate a vehicle off highway and also on highway gets an easy access to it,” Gerhardt said. “The capacity to increase hydrogen has to be increased in the next 10 years if we wish to reach a satisfying decarbonisation level.”
Alongside producing enough fuel, comes the question of building enough filling stations to satisfy demand for all the applications in which hydrogen machines are used. Currently, no such network exists, although other OEMs have come up with their own possible solutions to the problem, including JCB, which last year unveiled a mobile hydrogen refueller, which it proposed would work in the same way as fuel bowsers are used for diesel equipment.
4) Sustainability of hydrogen fuel
Meanwhile, hydrogen fuel will only count as a low-emission fuel if it is “clean” hydrogen. That means producing it using electricity generated from renewable sources. And producing it in sufficient quantities to make hydrogen combustion engines a mainstream option in industries like construction means that countries producing hydrogen as a fuel will need to ramp up their generation of renewable energy. “Further investment in renewable energy production should take place in every country where it is possible,” Gerhardt said.
Listen to the Diesel Progress/New Power Progress podcast interview with Gerhardt in full.
CONNECT WITH THE TEAM
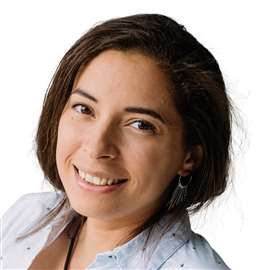
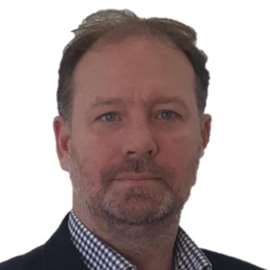