Leading the way: Japan's Watanabe Demolition
17 August 2008
Watanabe Demolition has been in the demolition business for almost 50 years, starting first doing demolition work by hand. Its first equipment was purchased from the American forces occupying Japan after World War II. The company was started by his father after the end of World War II, carrying out demolition by hand, but over the years Watanabe has developed into a heavily mechanised company, specialising in large scale industrial and urban demolition projects.
According to president Ryuichi Watanabe, turnover for 2008 is predicted to be of the order of 8-9 billion yen (US$70-85 million) making the largest demolition companies in the country. In this year’s D&Ri 100 listing of leading demolition contractors, Watanabe Demolition came in at number 26 on a reported turnover in 2007 of just over US$60 million.
“We are the largest contractor operating in the country – we are in fact the only company that generates a turnover greater than 5 billion yen – but it is impossible to even estimate what the total demolition/recycling industry in Japan is worth. What I can say that it is a growing market, both in terms of straight demolition work and also waste recycling. We work primarily with major clients in industry on major projects.”
In common with developments in the industry around the world where the disposal of demolition waste is concerned, Japanese legislators area fueling the growth in recycling, according to Mr Watanabe. “Japan in the past has had problems with the illegal dumping of demolition waste in addition to a chronic land shortage that has a serious impact on the availability of space for landfill sites, and the government has therefore introduced legislation to deal with the problem. For the last five years, demolitions contractors have had notify the Japanese government concerning the final destination for all such materials. On average, we would expect to recycle more than 90% of such waste, with the remainder going into landfill.”
“Waste is another reason behind our focus on large scale projects. Medium sized and small residential projects generate proportional more waste that has to be dealt with. A large office block, on the other hand, generates proportionally less waste volumes and what is generated is easier for us to reuse. Not to mention the fact that large projects generally a lot more profitable fro use, of course,” said Mr Watanabe.
Quite apart from official pressure and regulations, another reason for this high recycling rate is one that UK contractors, in particular, will sympathise with. In Japan, because of the pressure for land, the cost of landfill disposal is very high, a fact that naturally encourages demolition companies to recycle as much material as possible, according to Mr Watanabe. “As a result, a lot of recycled material currently goes to specialist recycling processors, who in turn ship it on to China – especially steel. Concrete is usually either used on site or used as sub base material for road construction.”
The company operates a fleet 80 excavators, mainly Kobelco and Hitachi, with a few Caterpillar machines, including Kobelco’s demolition flagship, the 65 m (213 ft) reach, 350 tonne SK3500 (of which Watanabe is taking delivery of a second model). This machine was specifically acquired to work in large industrial sites, such as factories and power stations. “There is a great drive in Japan to make the most of modern technology to maximise efficiency as well as to lessen the environmental impact of industry in general, and the power generation sector in particular. As a result, it will not be long before all our older generation power stations will be have been replaced by up-to-date facilities. This has meant that there has been and still is a lot of work available for us in the industrial sector, and the demolition of power stations in particular. Using the SK3500 on this type of large scale demolition jobs faster and more efficiently,” said Mr Watanabe
The company also operates a 180 tonne machine, two SK1600 160 tonne machines and 13 100 tonne class machines, 20 or more 20 tonne class and numerous other smaller machines.
The nature of Japanese construction, with its need to build in earthquake protection, fuels the need for large, heavy more powerful machines, according to Mr Watanabe: “The concrete is a lot stronger in Japan than I expect you normally find in Europe, and there is a lot more reinforcement, so we routinely need tools that are heavy enough and powerful enough to be able to cope. This is another reason why we require heavier machines because they are able to carry and power a tool of that weight. Using larger attachments results in a added benefit in that because of their size, they do not require as much maintenance as a smaller attachment would.”
Watanabe routinely using attachments weighing of the order of 4 tonnes or more on its standard demolition specification excavators. The trend in Europe and North America may be heading in that direction, but the majority of current ‘standard’ demolition excavators, including high reach rigs, are normally specified by manufacturers as having a maximum tool weight of 2.5-3 tonnes.
Watanabe works closely with its equipment suppliers, and from time to time provides a demand for a specialist machine to meet a specific demolition challenge. For instance, it currently working with Kobelco in the development of a special demolition machine that will be light, small but extremely powerful, able to carry a large powerful attachment.
This is the result of the fact that a lot of buildings in Japan and especially Tokyo, feature large multi-level basement complexes made from very thick, strong concrete. These are now beginning to reach the end of their life but demolition can be difficult because larger demolition equipment cannot gain access into them. “This type of demolition work is a relatively new challenge for us. Not only do we have to get machines into the site and deal with the concrete, but we also have to take account of the effect of the pressure from the surrounding soil on the basement walls while we carry out the demolition work, further complicating the demolition challenge,” said Mr Watanabe.
All in all, it is clear that while there are a few unique features of major demolition projects undertaken by Watanabe Demolition, the majority of the nature of the work it undertakes differs little from that found outside the country. The same short contract times, the same drive for recycling and the same need for efficient and productive equipment is apparent.
MAGAZINE
NEWSLETTER
CONNECT WITH THE TEAM
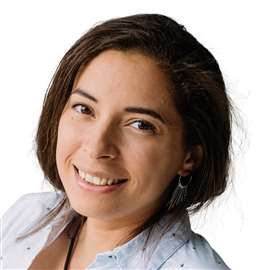
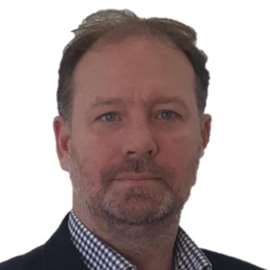
