Just Press Print: The Swiss startup planning to use robots-as-a-service for formwork
02 November 2023
Swiss startup Saeki is hoping to set up a robots-as-a-service model to 3D print custom formwork for construction companies. Lucy Barnard speaks to co-founder Andrea Perissinotto to find out how.
Inside an unremarkable building in the small Swiss town of Lupfig, a black metal box rather like a coffee vending machine makes a whirring sound. Automatic doors open and a chrome-coloured block slides inside.
The doors shut and a robotic arm whizzes round squirting out yellow goo so quickly that it builds before your eyes into an item resembling a flower vase. There is a flash of light and the doors open again, sending out the tray with the intricately completed vase on top.
Welcome to Saeki – an ambitious plan by three students from Zuchrich’s technology-focussed ETH university to create what could be the world’s first major robots-as-a-service model for 3D printing formwork for concrete construction.

“This black box is something we developed in house,” says Andrea Perissinotto, one of the company’s co-founders. “The plastic is melted down and then we deposit it layer by layer on a printing platform. And that’s how we build up these shapes in a pretty short amount of time.”
Perissinotto, who completed a degree in electronics and electrical engineering during the pandemic and who built his first 3D printer aged 12, set up the company in 2021 with fellow students Oliver Harley and Matthias Leshock, who shared his enthusiasm for robotics and 3D printing.
Although 3D printing has been around since the early 1980s, the process is now gathering steam in a variety of global industries. Already employed to make a whole range of products, from orthopaedic implants to components for aircraft, in recent years cement manufacturers and construction companies have been experimenting with using the technique to print whole buildings.
Details vary depending on the materials used and the type of product being created but the underlying principle remains the same. A robotic device squeezes out a thin layer of molten plastic, metal or concrete onto a base according to instructions from a computer programme. Then, as it starts to dry, another fine layer and another is added on top, building up objects which would be difficult or impossible to create by conventional methods.
Why use 3D printing in construction?
However, although long touted as a potential solution for slums and a rapid response to disaster-stricken communities, so far, the technology has only been used to build a handful of structures, most of which amount to little more than minimally functional single-storey pods and cabins.
Perissinotto and his partners quickly decided that formwork – the temporary moulds into which concrete is poured on construction sites – would be a major focus for their 3D printing business model due to the large size of the moulds needed and the difficulty construction firms are finding in recruiting the skilled woodworkers needed to produce custom-designed formwork.

“There’s no easy-to-use service where you can get a large part manufactured,” he says. “You can easily get something that is a couple centimetres 3D printed online – you get a quote immediately and get it printed and shipped in a week. But when we’re talking about a part that is five metres long and weighs half a tonne there’s nothing out there.”
Currently, unless formwork is required for something standard like a flat wall, most construction firms employ specialist carpenters to create custom formwork. Usually this is made from water-resistant timber shuttering kept in place by metal falsework poles and stabilisers until the concrete dries.
“Finding people that can build formwork is becoming harder and harder,” Perissinotto says. “Our customers have super skilled woodworkers now, but they are going to retire soon, and they haven’t managed to find replacements. And we can build the moulds in a more integrated way too. We don’t need to make fifty wood panels that are screwed and bolted together and which you need some sort of expertise to line up and assemble, it’s just three or four pieces that fit together like Lego – so even a non-skilled person can put it together.”
Perissinotto says that his 3D printed formwork currently costs around the same as nonstandard custom-made formwork made by traditional methods – costing between €500 and €1,000 per square meter. And the fact that it is machine-made means that it can include far more complexity.
More complexity
Currently the startup only has two robots which work independently creating formwork which is either shipped directly to construction companies for use on construction sites or to manufacturers who then pre-cast the concrete elements themselves and sell them on to contractors.
However, the company’s ambition is not to act as a 3D printed formwork mould manufacturer but rather to sell subscriptions to its services for 3D printing formwork (and other components). Under this ‘robotics as a service’ business model, Saeki plans to develop a number of 3d printing hubs, each of at least 10 robots so that customers around the world can then pay to book time with its robots to fulfil regular orders.

“In the beginning we thought we would just build the machines and sell them but then we realised that it makes no sense both to us and to the customers,” says Perissinotto. “The problem with buying a machine is you’re going to have one machine that can only print one object at a time – and that requires one person to operate it. And to do that requires a whole new set of skillset - from the design side, to the code preparation, to the knowledge of materials. Under our model, you send us a request for 50 components, and we can have five robots start at the same time because we have the printing capacity to then deliver parts five times faster.”
In August the company announced a US$2.3m seed funding round led by Swiss venture capital company Wingman Ventures which, along with some Swiss government research funding, will enable the company to set up its first ‘hub’ – a mini-factory of at least 10 robots which it hopes to establish in Switzerland by the end of 2024.
After that, Perissinotto says, the company intends to raise another financing round in order to set up further ‘hubs’ around the world, starting with the USA but also looking at the Middle East.
And, he says, if 3D printed formwork is adopted on a large scale, it has the potential to fundamentally change the construction and design process and actually reduce the amount of concrete used.
“Up to 80% of the materials used in a modern building do not actually need to be there,” Perissinotto says. “There is no need to cast 30 centimetres of concrete all the way through a building, it’s just cheap to do it because concrete is cheap. By optimising the geometry of a building and the loads that go into it, you can actually take a lot of concrete out of the building. At the moment, these connection details that are very expensive because if you create an optimised column, it’s going to have some sort of intricate details and it’s just cheaper to cast a thicker slab. But with 3d printed formwork, these geometrical limitations are not limitations anymore.”
MAGAZINE
NEWSLETTER
CONNECT WITH THE TEAM
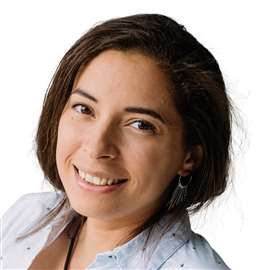
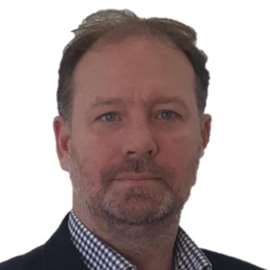
