How do you dismantle a 70-metre-high city building without anyone noticing?
03 July 2025
As urban density increases and public tolerance for disruption declines, demolition contractors are turning to methods that make buildings disappear quietly, cleanly, and almost invisibly. The recent dismantling of Milan’s Hotel Michelangelo by Italian contractor Despe offers a case study in controlled removal under public scrutiny.
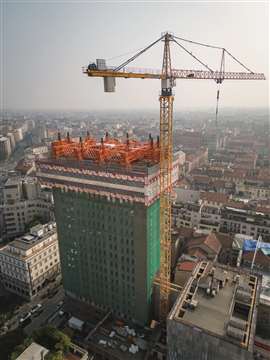
In the heart of Milan, next to the city’s Milano Centrale railway hub, an 18-storey tower disappeared. Not in a blaze of noise or a cloud of dust, but methodically—floor by floor—inside a shroud of scaffolding and steel.
Most passersby never realised it was happening. This was not demolition as spectacle. This was demolition as silence.
High rise challenges and urban complexities
The project, led by Despe, involved the deconstruction of the former Hotel Michelangelo in Milan, Italy.
Located adjacent to the Milano Centrale railway hub, the Hotel Michelangelo complex comprised an 18-storey, 70-metre-tall tower built in the 1960s, a nine-storey, 35-metre-tall rectangular addition, and a four-storey flat-roofed section that wrapped around the other buildings.
Once a prominent part of the Milan skyline and more recently known as a Covid quarantine facility, its removal presented the typical constraints of dense urban work—tight logistics, close residential proximity, and pressure to minimise noise, dust, and disruption.
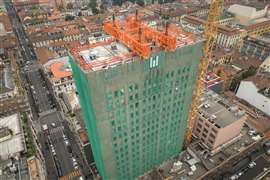
Fully enclosed on two sides by residential buildings and directly bordering the busy streets of Via Lepetit and Via Scarlatti on the others, Despe’s task was to demolish the entire complex—which was “characterised by reinforced concrete structures and horizons, with pillars and wall beams of considerably thickness”— under tight logistical and environmental constraints.
The client’s primary requirements were that the project had to be executed with minimal disruption, noise, dust and vibration, while also allowing for an accelerated programme to enable the site to be redeveloped.
Phased execution
The first step Despe took to achieve this, was to increase the limited operational space available. The flat-roofed building was partially demolished to create a staging and access area along Via Lepetit—a key move that enabled subsequent operations.
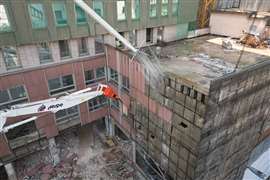
As the aggressive schedule meant that the structural demolition had to be overlapped with the strip-out phase, Despe adopted a dual-method approach.
The central tower was deconstructed using the company’s proprietary Top-Down Way (TDW®) system—a self-descending modular containment system.
Installation of the TDW® on the roof of the 18-floor-high central tower, saw the use of a 90-metre tower crane. While deployment of the crane required the brief closure of Via Lepetit, one of the bordering streets, it was essential for assembling and operating the TDW® unit, which enabled floor-by-floor deconstruction from the top down. This enclosed system contained the debris and noise, aligning with client requirements for minimal disruption.
In parallel, the nine-storey extension was dismantled using mini-excavators from the top down. By splitting the demolition methodology across the site, Despe was able to progress both parts of the project simultaneously and maintain control over logistics and environmental outputs.
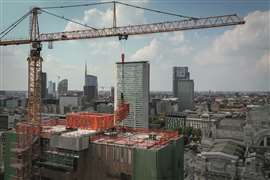
Tools, logistics, planning
The constrained nature of the site also influenced how equipment and labour were deployed. Despe used machines ranging from 3 to 40 tonnes, including two 10–14 tonne excavators, a 20-tonne crane dedicated to TDW® operations, and high-reach machines to complete the dismantling of the flat-roofed building once sufficient access had been created.
Laser scanning and BIM modelling supported the project’s planning and execution, enabling precise sequencing in a highly congested area.
The workforce peaked at just 14 people on a single shift, reflecting the controlled and phased nature of the works. No health and safety incidents were reported during the operation.
Material recovery
In total, Despe removed approximately 72,000 cu m of structure: 41,000 cu m from the tower, 16,000 cu m from the nine-storey block, and 15,000 cu m from the flat-roofed section.
More than 25,000 tonnes of inert material was recovered, with the company reporting a 100% recycling rate. Clinker wall tiles were manually salvaged from the tower and are expected to be reused in the site’s redevelopment.
The full project was completed in under seven months, with the tower deconstruction phase taking approximately four.
The site will now be redeveloped as part of a broader urban regeneration programme linked to the 2026 Milan-Cortina Winter Olympics. A new vertical structure will replace the hotel as part of the city’s densification strategy.
CONNECT WITH THE TEAM
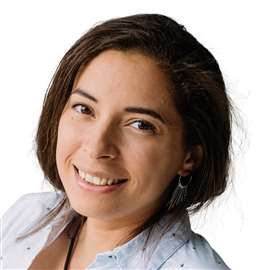
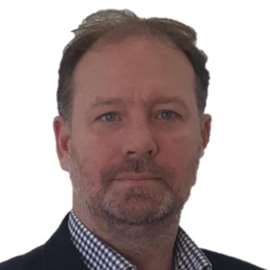