How can decommissioning safety be improved?
20 July 2022
Doug Thomas, vice president of project management at US contractor Independence Excavating talks to D&Ri.
When decommissioning power stations, every job is different – but what is common to them all is that safety is the number one priority.
Coal fired power plants are a challenge that you have to plan and account for. Environmental is always a challenge – you have to be aware of the different chemicals, the different ash, the components, and the regulatory requirements are for the area that you are working in.
The schedule can also be a challenge, depending on the owner’s requirements, the overall objective and what they want to do with the property afterwards.
And of course, there is the budget. We all want to do it faster, better, cheaper. But we all want to do it safely, effectively, and with the owners of the plant being happy at the end of the job.
At Independence, we are up to more 30 power plants to date, and we working two actively right now.
The path for the expertise has really been in the understanding of the systems. I think that is what we and our competitors have done well in the industry. You certainly must have the planning and the foresight. Whether that is daily for the job hazard analysis of what the guys are doing for that day, or the overall work plan for the site. Then you need to understand the owners of that facility and the people who ran it for 30 or 50 years.
My position is over the civil and demolition divisions of our company.
Customer requirements have changed as the breadth of their knowledge has increased, and we have worked with some fantastic consultants that help the owners along in accomplishing their objectives.
Training in demolition
The NDA (National Demolition Association) has done a very good job, especially in the past five or 10 years, in its education programme and there are even some exciting things that are coming up to bolster it even further.
It is definitely better to have these resources and procedures. It gives you the tools to manage it better.
Stakeholders in the project change with every project. Obviously there is the owner. There may be a consultant involved. But then you get into other things, you get into different departments within the owner’s entity. Whether it’s a maintenance department, an environmental department, or accounts or contracts.
There are some community groups out there with a vested interest in the demolition of the plant and how the project will be reused.
One recent project led to a significant loss of jobs in the community, so the owner developed a hiring preference to at least get some of those jobs back in the demolition, which was a great success. We hired over 50 people from the local area, and some have joined the workforce. They go all over the country with us. That is a success story you always want to hear.
With so many power stations disappearing, the industry has become very competitive.
The Electric Power Research Institute has forecast that work will continue into the 2030s. There are a lot of these power stations coming down just now, but there are a lot of them still to come down in the future. The industry is going to be a niche market for a while.
Recycle from decommissioning
All contractors involved in decommissioning power plants say we are the best, Independence included. But there is a core group of very good demolition contractors, because you can’t just put a high reach in the air and wreck a power station.
Whether it’s Independence Excavating, or whether it’s somebody who works alongside us, we do really have a good niche market and a definite a growth area.
We work on a lot more of the coal fired plants than nuclear. They both require a significant amount of planning, of engineering, critical work and evaluation of job hazards to keep our guys safe through the process.
The steps that we have taken with safety, I would love to say it’s specific to power plants but quite frankly it’s not.
It really comes down to pre-test planning. How is the station going to come down? Where do I need to plug in a professional engineer to really analyse the structural integrity and to make sure that those steps are taken? And then from there, you have the safety personnel in the field, to watch and observe and ask the people who are performing this work what they see as the hazards.
To get the buy in that way takes not just a good safety department but also a good workforce to really embrace it.
I think there are a lot of opportunities to recycle from decommissioning power plants. On most of our jobs – maybe all our jobs – you can see recycling rates well over 90%, because of all the things you can do with the metals and alloys, and certainly because of everything you can do with the concrete.
To put concrete into a landfill or just a fill is not as effective, but if you can crush it and use it as road base, or as back fill within the site, it is really beneficial.
How can project flow be improved?
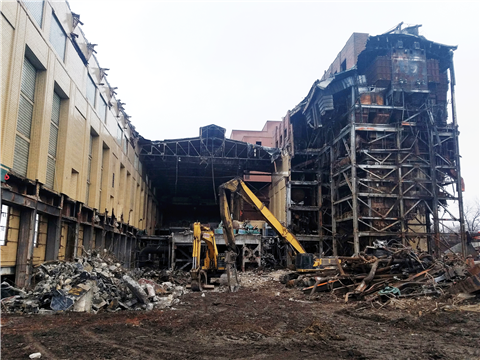
In terms of the project, recycling is definitely a conversation to have up front, plan for and be ready to address. It is similar to, thought not as important as, safety and planning.
To have a plan of your recycling is going to make the project flow even better and it can be an asset of the project. If you have your eyes open going into the project it puts you that much further ahead.
There are only so many power stations you can decommission but there are a lot of them. Power stations decommissioning is going to carry us for several years to come, but there are also a lot of other industrial demolition projects out there as well.
To have the diversity and maybe to take some of the lessons we are learning from power stations and apply them to other facilities, there are other types of work and other types of industrial facilities is what makes us stronger and what makes us better.
To say, look, we could take some of the lessons from the power industry and apply them to the steel milling industry, the automotive industry, the chemical manufacturing industry, whatever, and to have some of those programmes for a safe job all around, ultimately that is what we want.
That is absolutely one of the things that we do as a company and that the NDA does as an association.
Even industry wide, I have talked to some of my other competitors and co-workers to really bolster our lessons learned programme, because that programme can be an integral part of safety, but it can also be an integral part of management overall, of unforeseen environmental issues, contract issues, definitions within specifications.
All of these are lessons that we can learn. We have a very robust programme within our company to take the lessons that we learn on one job and apply them on another job.
Effective decommissioning
The NDA has a similar programme where we are trying to share some of those lessons among all of us of how we manage our issues and how we get through them.
And a lot of our competitors have similar programmes because all we want to do is get better and more efficient.
It makes owners happier, it makes a contractor happier, it makes our job much more effective.
CONNECT WITH THE TEAM
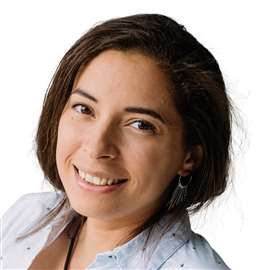
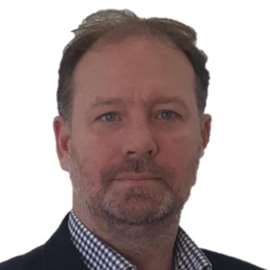