D&Ri Equipment section, May-June issue
03 June 2021
The largest short radius yet
Kobelco Construction Machinery Europe has launched its new – and largest – short radius excavator.
The SK380SRLC weighs over 36 t and its 6.2 m (20 ft 4 in) long boom has a maximum lifting capacity of 12.4 t (12.3kg) at a ground level.
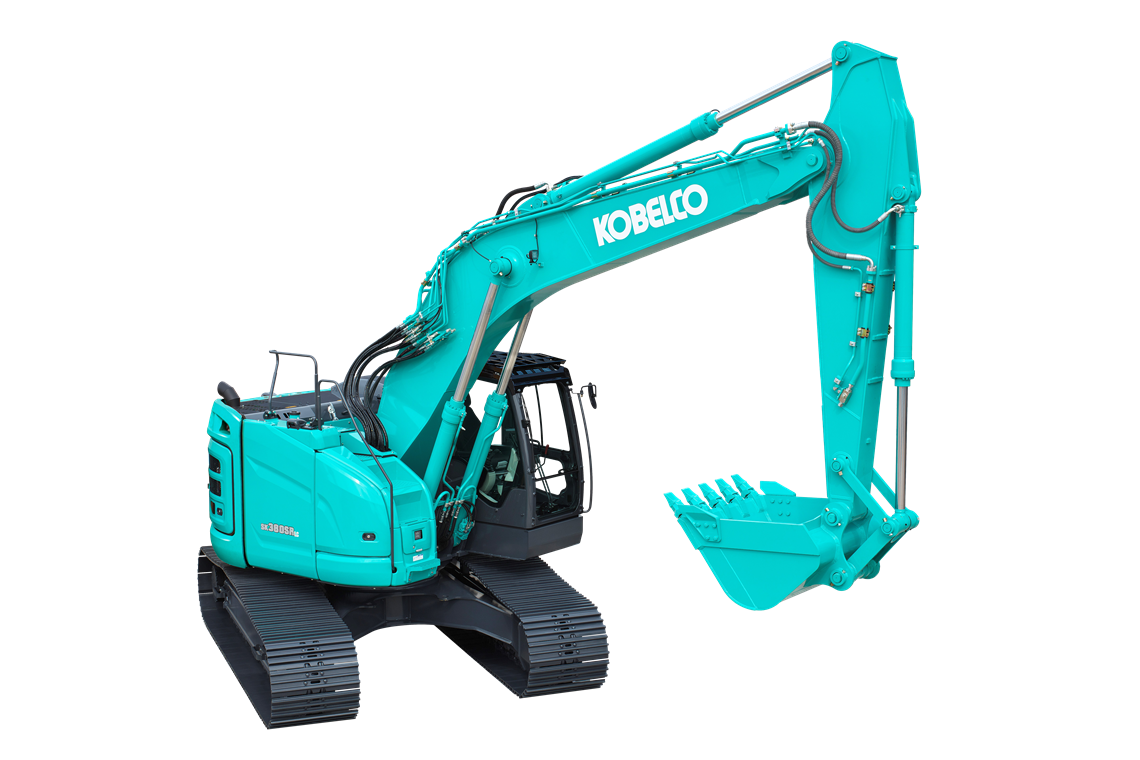
The Stage V compliant machine is equipped with a turbocharged Hino diesel engine that provides 200 kW of power and has a Power Boost mode, which provides 10% more power.
The SK380SRLC’s powertrain delivers a drawbar force of 314 kN for smooth operation, making it suitable for both urban projects and for use on rough or sloping terrain.
Peter Stuijt, product manager at Kobelco, said: “The arrival of the SK380SRLC is a result of extensive market research and customer feedback, coupled with Kobelco’s extensive experience in innovative technologies.
“We’re seeing more demand for Short Radius machines, due to increased requirements for urban infrastructure and utilities, and the SK380SRLC offers all the benefits of a heavy machine, including high power and increased lifting capacity, but in a much smaller working footprint.”
Inside the cab, the short radius excavator features a colour LCD multi-display screen. Operators can use the device to access machine data such as fuel consumption, maintenance intervals, digging mode and other important information at-a-glance.
The display screen also gives operators up to ten pre-set attachment settings for a range of applications including breaking and other demolition tasks.
Revamped Bison
Northern Ireland-based compact crushing and screening equipment specialist EvoQuip has launched the revamped Bison 120 jaw crusher, with enhancements including a Deutz 2.2 L3 Engine Stage V engine.

With almost 100 units sold globally, the Bison 120 has been a core product in the EvoQuip portfolio since its inception five years ago.
The revamped version has been tested at various sites in the past six months, including a 1960s farmyard barn and a house demolition.
EvoQuip, part of the Terex Corporation, said the 120 has been specifically designed for operators for whom versatility, manoeuvrability and transportability are of key importance, and that it is small enough to fit inside a container for transport but strong enough to withstand the toughest of applications.
The Bison 120 features a 680 x 400 mm (26.7 x 15.7 in) single toggle jaw crusher. The jaw is driven hydraulically, allowing the customer the ability to reverse the crusher to clear a blockage as well as being able to run in reverse permanently for sticky applications such as asphalt.
Mecalac launches backhoe loader
Mecalac Construction Equipment has completed its range of sideshift backhoe loaders with the launch of its Stage V compliant TLB880 model.
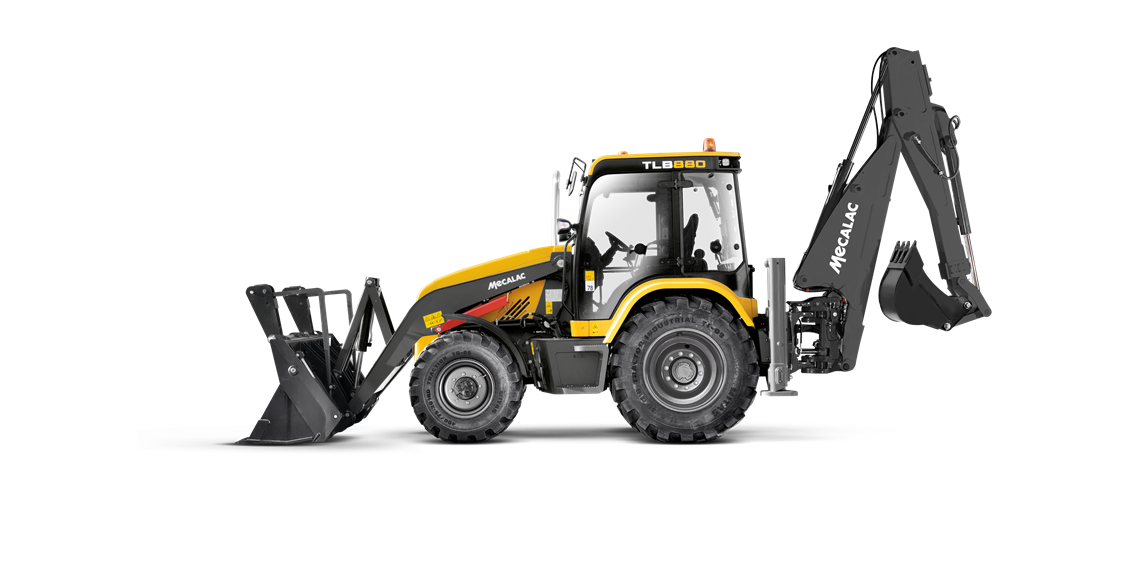
Joining the manufacturer’s TLB870, TLB890 and TLB990 backhoes, the new model features a Perkins 904 turbocharged diesel engine and delivers 74.5 kW (100hp) of power and 430 Nm of torque.
Mecalac said the heavy-duty sideshift model had been designed to provide fast cycle times and precise operation. It incorporates a closed-centre hydraulics system that delivers a maximum flow rate of 143l/min and an operating pressure of 250 bar.
A maximum digging depth of 4.4 m (14 ft 6 in) makes means the machine is suitable for range of applications in the general construction, civil engineering, highway maintenance and utilities sectors.
It also offers road speeds of up to 38 km/h (24 mph) and is available with either a four-speed synchro shuttle transmission or a servo power synchro powershift gearbox.
While the exterior of the cab is equipped with front and rear LED worklights and a transport lock, the interior is fitted with ergonomic controls for operator comfort.
The model, which available with a range of attachments and optional extras, also has a fully tilting hood for easy maintenance access.
Powerscreen takes up challenge
Powerscreen, the provider of mobile crushing and screening equipment, is responding to the industry’s decarbonisation challenge by providing solutions that work towards minimised environmental impact and greater sustainability.
The company’s decarbonisation story begins with the introduction of the concept of mobile crushing and screening, has evolved to increase fuel efficiency and looks to the future with Powerscreen’s electrification strategy, including an exciting, brand-new concept for the future of crushing and screening - the Eco-Warrior battery powered screener.
Neil Robinson, Powerscreen product and applications manager said: “Some may view this topic as a recent trend, but for Powerscreen, decarbonisation is multi-faceted and has always been at our core.”
Powerscreen has evolved its product range to reduce environmental impact by making its crushing and screening equipment as fuel efficient as possible, using direct drive systems for its crushing range and improving engine capabilities and drive-line design for its screening range.
Kleemann launches mobile jaw crushing plant
Germany-based equipment manufacturer Kleemann has introduced the Mobicat MC 110(i) EVO2 mobile jaw crushing plant following further developments of its predecessor.
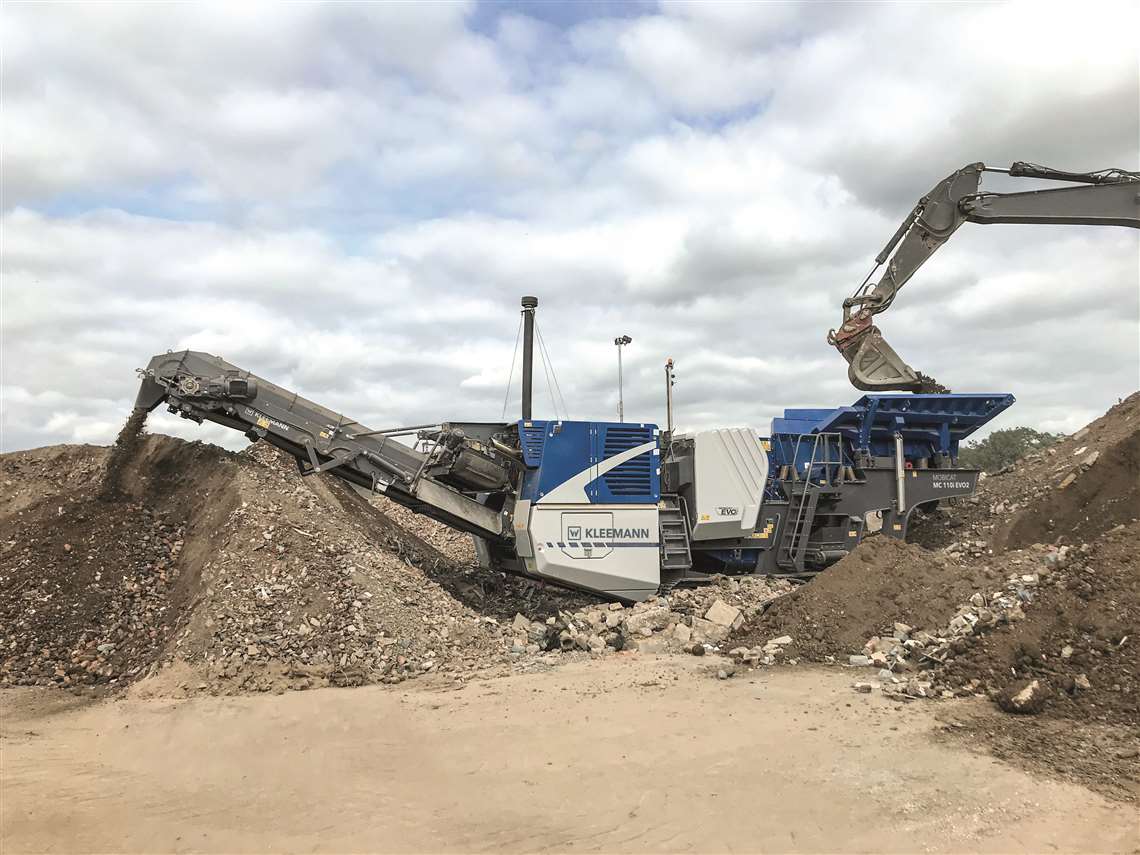
With this launch, Kleemann said it has a mobile jaw crushing plant “of the new generation” that offers users “groundbreaking technologies for optimising all areas of a typical workday”. Specifically, the focus is on economy, operability and sustainability.
During the development of the mobile jaw crusher plant, Kleemann concentrated on the requirements of demolition and building companies, contractor crushers and quarry operators. With an hourly output of up to 400 t/h, the crusher is said to meet the requirements in the medium output range. It can also be used in a range of quarry and recycling application, where the emphasis is on effective coarse crushing.
A further result of the latest developments is that the transport height of the crusher reduced by 20 cm (8 in) to 3.40 m (11 ft 1 in). Relocation is now possible with simplified transport by means of semi low-loaders. The start-up procedure itself takes only around 10 minutes and includes set-up times for flaps, belts and feed hopper.
A further feature is a new two-stage overload system. It effectively prevents blockages and material bridging that can lead to unwanted downtimes. If uncrushable material enters the crushing process, the CSS opens twice as fast as with the predecessor plant or, as an option, even up to 40 times faster, while the new digital solution Spective Connect sends all important plant data to a smartphone.
CONNECT WITH THE TEAM
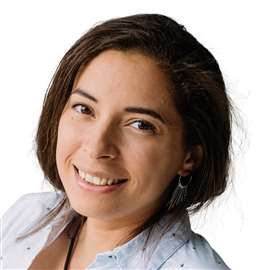
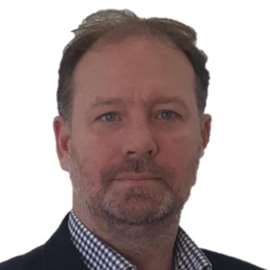