Crushing – Making a contribution
22 March 2021
A37 t R1100DS impact crusher from Austrian manufacturer Rockster has been identified for a vital role in improving national recycling rates by Chinese company Kebao Construction Machinery Leasing.
Based in Chongqing in the south west of the country, Kebao has been active for 10 years renting machinery such as jaw crushers and scalping screens.
CEO Ran Maohe said the new crusher had to be easy to transport, reliable and ready to use quickly: “Thanks to the compactness of our new R1100DS impact crusher, we are able to transport the machine, including the screening system, over our winding mountain roads using an ordinary flatbed truck.
“The crusher set up time is extremely short due to the saved settings. Our machine operators are also able to operate the crusher very quickly thanks to the intuitive and simple handling. We only rent our machinery with our own trained staff, which of course benefits the efficiency and longevity of our machines. “
As well natural stone, the new Rockster crusher is used for processing recycling demolition debris.
“In recent years, China has generated more than 1.5 billion t of construction and demolition waste annually, with a recycling rate still below 5%,” said Ran Maohe.
“By recycling with a crusher like our R1100DS, most of this construction debris could be reused and the positive effect on the environment and economy would be enormous.
“Relevant departments of the Chinese government have passed laws that require construction waste to be properly processed so that it can then be used as recycled building materials, mainly for substructure projects. This is our great opportunity to contribute.”
Meanwhile on the other side of the world, the Hawaiian island of Oahu to be precise, Rockster has supplied a R700S impact crusher to Alakona Corporation, an asphalt paving and maintenance firm founded almost 40 years ago by Mervyn de Wolff. Based in Honolulu, it serves Oahu and neighbouring islands with a team of over 20 people headed by Mervyn’s son Arist, and has clients including government organisations, commercial enterprises and property managers. In recent years business has shifted towards recycling.
Alakona owns several machines necessary to the core business like pavers, rollers, loaders, excavators, slurry and seal coat applicators. When it searched for a crusher, the focus was on compact machinery below 25 t.
”We are so flexible in terms of processing different aggregates and the material we produce with our crusher is of high value,” said Arist de Wolff.
“We do also like the fact that the return belt can be turned aside, and we can make another fraction, as well as the fine side belt that can be pulled off. The screen box is also very beneficial as it allows us to produce different material sizes by just switching some screens. There are some options that others don’t have, and we are very enthusiastic about the hydrostatic drive.”
Logical step
Alakona views the move towards recycling as a logical step.
“Obviously, natural rock isn’t going to be there forever,” said Arist.
“In future we would have to ship it in from the mainland. Sustainability is the key factor. We need a lot of material for sub bases, base coarse or backfills. Using Reclaimed Asphalt Pavement (RAP) instead of natural aggregate saves resources and money.
“Moreover, RAP contains bitumen, it is like a glue, holding everything together and giving more compaction”.
With a screen box and return belt, the Rockster R700S weighs 22,815 kg (50,300 lb) and Alakona said it can be transported with the company’s own flatbed truck without the need for transport permits.
“We are able to crush so many kinds of material,” said Arist de Wolff.
“Within four days of training this summer, we crushed RAP, coral, concrete and basalt. There are so many possibilities for a lot of different customers like construction companies, privates and of course municipalities. You would think that people on an island would be more aggressive about researching, testing and using recycled material, but they are hesitant in trying new things. It needs to be pushed more and people need to understand that this is the future. There needs to be recycled material especially in construction fields where we could save so many natural resources.”
Material disposal costs
Italian manufacturer MB Crusher can also point to recent international applications as it aims to help the road construction industry face the challenges associated with high hauling and material disposal costs while also protecting the environment.
Anyone with an ongoing road construction project knows this industry’s hurdles on any job scale, from the reconstruction of a main road to a small side road. The same restrictions also affect those who process and distribute bituminous conglomerates.
MB Crusher said that through its presence on job sites worldwide, it has focused on this weakness and transformed it into a new advantage.
The company added that its mobile crushers can be mounted on any brand and sized heavy machinery on the job site, transforming the equipment into a powerful crusher.
Recent applications include a company in Chile that, using an MB-L200 Crusher bucket, recycled material to use as a sub-base. In Brazil, a company used a BF70.2 crusher bucket to make reclaimed asphalt ready to use on the job site.
And the landing strips at Reykjavík airport in Iceland, were rebuilt by using the old asphalt as a base material, thanks to the use of a BF70.2 crusher bucket.
According to MB, each bucket is designed to adapt to all requirements of a job site easily, It can be paired with any heavy equipment, it crushes any type of asphalt and hard material and does not require specialised mechanics for its maintenance.
Modular concept
Swedish manufacturer Maskin Mekano says the ambition behind its modular concept is to combine the best from stationary plants with the flexibility of a mobile one.
In production, these machine units on their high jacking legs resemble stationary plants while being very easy to move between different workplaces. With modules for feeding, crushing, and screening by Maskin Mekano, the company says the user can an build optimised plant with high capacity.
The company’s programme of modular machines features electric drive; interlocking control systems and emergency stop loops; user-friendly and safe service work; secure establishment and de-establishment; no removal of machine parts before moving; loading and unloading without lifting assistance; and a transport width of under 3 m (10 ft).
The CH440-PS cone crusher is an important cog in Maskin Mekano’s in modular range, where there is a VSI crusher, feeder stations and screening units. The machine is a conveyor in/conveyor out version with a pre-screen and it is equipped with an on-board return conveyor that makes it compatible with Maskin Mekano’s final screen SH 1503 for closed circuit.
The CH440-PS is equipped with Sandvik’s CH440 cone crusher. Before entering the crusher, the material is loaded on a pre-screen with an on-board conveyor that either takes a 0-size material out of the process or runs the material by-pass to the conveyor under the crusher. The crushed material is loaded to the docked screen SH 1503 and the return is handled with an on-board swivel conveyor.
Single lifting point
United Kingdom-based Dragon Equipment has launched the hybrid CR300H, which has jaws that can crush up to 7 t/hr into reusable hardcore and was recently shortlisted for a World Demolition Award.
The CR300H weighs under 780 kg (1,720 lb), has a single lifting point, and multiple tie-down points. The manufacturer says it can be transported in the back of a van, makes it easy to attend multiple sites within a day and make more efficient use of time. Its 700 mm (28 in) width also makes it suitable for jobs with difficult or narrow access, or where access is through an existing building.
Said to offer more power, better fuel efficiency and lower emissions under high load conditions, it uses the same Vanguard 400 engine as its petrol-powered counterpart.
According to Dragon, the inspiration for the hybrid machine was taken from the automotive industry. Hybrid technology was applied to the crusher to achieve the desired output, so the hybrid powertrain gives the CR300H precise power for the job at hand while optimising fuel efficiency.
The hybrid technology is described as dramatically reducing emissions produced during crushing, while also alleviating air pollution concerns.
Flow control valve
The Xcentric Crusher is a crusher bucket with patented technology, for rock crushing and recycling of materials. The Spain-based manufacturer says the new series models are characterised by a different operating mechanics system from the previous ones, and for being much simpler in terms of internal assembly.
The new granulometry adjustment system offers rapid change, together with a greater possibility of output sizes.
Having no drain line in the hydraulic motors and the flow control valve is said to make the equipment easily interchangeable between excavators, with a very low risk of failure in case of poor hydraulic adjustment.
The maintenance-free power train increases the reliability of the machine in the long term. And the replacement of the jaws in case of wear is now said to be very easy, because the bucket can be opened completely to perform this operation.
- Article first published in the January-February 2021 issue of Demolition & Recycling International
CONNECT WITH THE TEAM
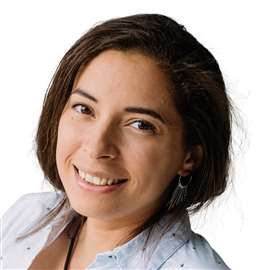
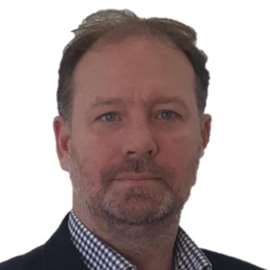